Decomposing refrigerants with industrial waste
24th July 2024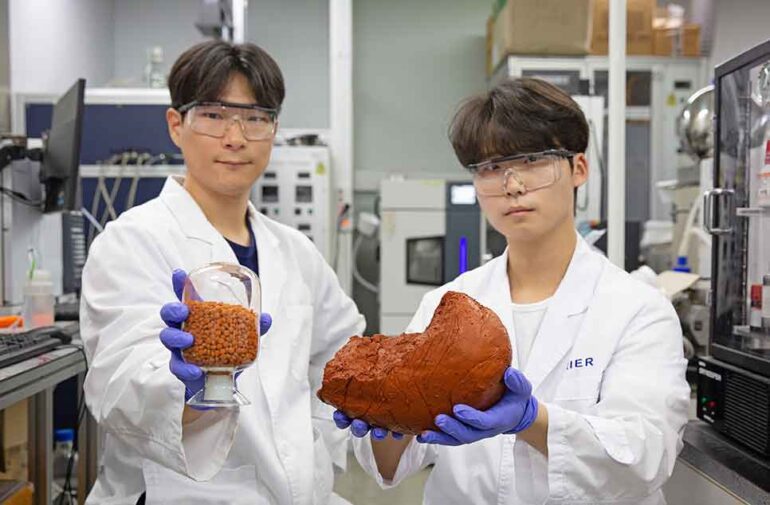
SOUTH KOREA: Researchers from the Korea Institute of Energy Research (KIER) claim to have developed a technology to decompose R134a refrigerant using an industrial waste product.
The process is seen to have a number of potential environmental benefits: in addition to lowering greenhouse gas emissions, it utilises a toxic industrial waste by-product and is a less energy consuming alternative to current HFC destruction methods.
Dr Lee Shin-geun’s research team at KIER’s Hydrogen Composite Material Laboratory succeeded in decomposing the HFC R134a with 99% efficiency by using “red mud”, an industrial waste generated during the aluminium manufacturing process, as a catalyst.
Red mud is a by-product left over after recovering aluminium oxide from the mineral bauxite. It contains oxides of iron, aluminium and silicon, giving it a red colour. More than 200,000 tons are produced annually. Most of the red mud is currently disposed of by landfilling in the ground or lakes, but it is highly alkaline and contains heavy metals which cause soil and water pollution problems.
Meanwhile, R134a is mainly processed through combustion and plasma methods, but combustion generates secondary pollutants and the high-temperatures required using plasma requires a lot of energy and equipment costs.
To overcome these limitations, the research team developed a catalytic decomposition technology that can be processed at lower temperatures than plasma. In particular, the research team focused on the fact that various metal components, such as iron and aluminium contained in red mud, can interact to form a strong and stable refrigerant decomposition catalyst.

Red mud has a porous structure with a large surface area per unit mass and high thermal stability, which allows the reaction materials to flow efficiently and suppresses physicochemical deformation and destruction of the catalyst. In addition, it acts as a support that improves the durability and activity of the catalyst by creating an environment favourable for interfacial phenomena for catalytic reactions such as adsorption and electrophoresis.
In order to further improve the decomposition performance, the research team induced the interaction between calcium, silicon and aluminium components through a simple heat treatment process and formed tricalcium aluminate and gehlenite composite materials. This is a material used to increase the strength of cement, strengthens the bonding of catalyst particles, and increases the reaction area, thereby improving the decomposition performance.
The hydrogen fluoride generated by the decomposition of R134a reacts with calcium oxide to form calcium fluoride. The chemically stable calcium fluoride forms a thin film on the surface of the catalyst and acts as a shield to protect the catalyst, preventing deactivation.
The catalyst developed by the research team is said to have shown excellent refrigerant decomposition performance by maintaining a high decomposition rate of over 99% for 100 hours. In addition, it can be produced at 1kg per hour through a simple drying and crushing process, making it easy for mass production. In particular, since it is made by recycling industrial waste, there is no cost for raw materials, and waste disposal costs can be reduced and additional revenue can be generated.
“Red mud is a strong alkaline substance that can cause serious environmental pollution when released into the surrounding environment, but there was no proper technology to process and recycle it,” said Dr Lee Shin-geun. “The catalyst manufacturing technology we developed not only reduces environmental pollution by recycling waste, but can also decompose refrigerants, which have a strong greenhouse gas effect, with excellent performance.”