Daikin/Hitachi use IoT for skill transfer
26th September 2017JAPAN: Air conditioning manufacturer Daikin is to collaborate with Hitachi to establish a next-generation production model utilising IoT in order to support skill transfer from expert workers.
From next month, Daikin says it will introduce a system that employs the advanced image analysis and other technologies of Hitachi’s IoT platform Lumada to enable digitalisation, comparison and analysis of the skills of workers on the brazing line at its residential air conditioning factory in Shiga. In this way it intends to ensure consistent quality, improving productivity and developing human resources at production locations worldwide.
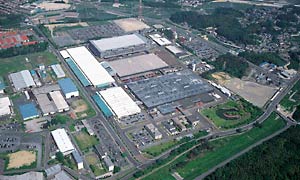
Hitachi’s Lumada technology uses sensors on factory machinery and infrastructural equipment, linking them via networks. This data analytics and machine learning can support predictive maintenance and the optimisation of manufacturing processes.
Daikin and Hitachi say they will demonstrate the viability of a production model using this system, to begin full-scale operation of the system in actual manufacturing workplaces during this fiscal year. The aim is to expand applications of the system to other Daikin factories and manufacturing processes worldwide.
As global competition in the manufacturing industry intensifies, Daikin says it needs to shorten product development time and achieve quicker launch to market. It also sees a need to improve quality and increase productivity globally. Skill transfer from expert workers is vital.
In order to improve and equalise quality worldwide, Daikin has worked for many years to train new workers and transfer skills of expert workers, with efforts centring primarily around core skills such as brazing, lathing, sheet-metal working and arc welding.
Meanwhile, Hitachi has worked to provide solutions that will raise the level of manufacturing capabilities through the application of IoT platform Lumada using operational technology (OT), IT and digitalisation of the manufacturing workplace.
The system detects signs of deviations of workers’ motion in front-line and facilities failures to compare and assess the skills of expert workers and trainees. Based on validation tests conducted so far, Daikin and Hitachi have constructed a Brazing Skills Training Support System.