Are 3D printed heat exchangers viable?
8th September 2015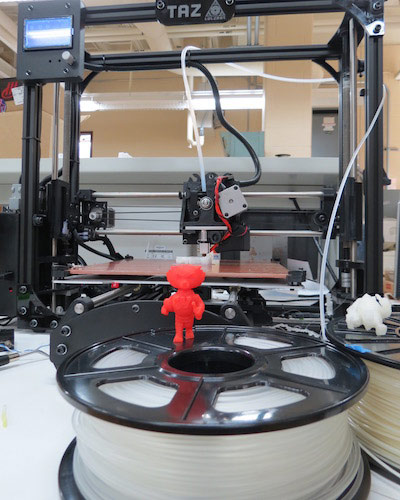
USA: A team at the University of Wisconsin-Madison is working with new materials in an effort to produce a viable energy efficient 3D-printed heat exchanger.
The capability of a heat exchanger to transmit energy is determined both by its geometry and the material from which it is manufactured. The metals used to produce conventional heat exchangers transmit heat highly efficiently, but may only be machined in a limited scope of shapes. While heat exchanger design is crucial to efficient heat transfer, the optimum shape for heat transfer may not be feasible for conventional manufacturing.
“3D printing allows us to think a little bit differently,” says Natalie Rudolph, an assistant professor in the Department of Mechanical Engineering at the University of Wisconsin-Madison and an expert in polymer engineering and 3D printing. “The current generation needs to relearn what is doable with fewer manufacturing restrictions than conventional processes.”
3D printing allows designers to create a spectrum of shapes unencumbered by traditional manufacturing restrictions. Unfortunately, 3D printing with metal is prohibitively expensive and heat exchangers made from plastic are innately limited due to the material’s poor thermal conductivity.
However, as Rudolph’s colleague Tim Shedd and a group of students demonstrated in their 2014 prototype of a 3D-printed heat exchanger, the freedom in design already allows significant improvements. Rudolph hopes to take it one step further by 3D printing heat exchangers made from plastic polymers blended with a filler material, such as graphene or ceramic, to additionally increase the heat exchange capabilities of the materials.
The researchers hope to produce a prototype heat exchanger within 18 months using a 3D printing technique called fused deposition modelling (FDM). This project is supported by funding from the US Department of Energy ARPA-E program.
FDM historically has been seen as useful for producing prototypes, yet not applicable to large-scale industrial applications. Rudolph, however, says FDM has potential as a manufacturing technology. The low-cost of FDM printers could allow for decentralised industrial production. Rather than manufacturing a part in Madison, for example, and shipping it cross-country to the end user, Rudolph envisions a future where power plants print custom heat exchangers or replacement parts on site to fit the needs of their facility.
To facilitate future large-scale applications of the technology, Rudolph and colleagues have initiated collaboration with Oak Ridge National Laboratory, which recently made headlines by producing a 3D printed car.