Bitzer to offer remanufacturing
25th April 2014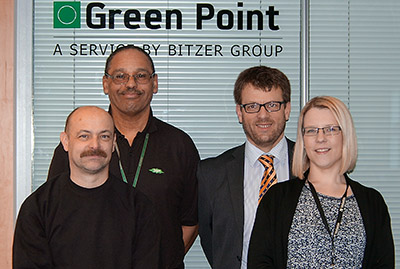
UK: Bitzer has taken a wholehearted leap into refrigeration compressor remanufacturing with the official opening yesterday of Green Point UK.
Eight years on from the German compressor company’s first remanufacturing site in France, and now with 30 similar locations around the world, the technology has been brought to the UK with a 2,600m² facility at the UK company’s headquarters in Bletchley.
Although the remanufacturing service has been available to UK customers through the French facility since 2009, it is no surprise that the service has now been brought close to home. With the UK representing the largest European market for compressor remanufacturing, it’s only a surprise it hadn’t happened sooner.
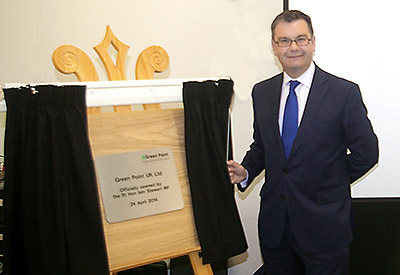
The establishment of Green Point UK underlines Bitzer’s long term commitment to the buoyant and growing UK remanufacturing market which is valued at around £13m per annum. According to BRA statistics, on average, in excess of two remanufactured semi-hermetics are sold in the UK for every one new machine. On the larger units, in excess of 50hp, five times as many are sold.
Green Point UK will offer remanufacturing on all Bitzer recips and screws with an eventual capacity of 1,800 units per year. Remanufacturing will also be offered on other manufacturers’ reciprocating compressors.
“Remanufacturing services for compressors already exist in the UK and indeed there is an established market. We, however, are offering something different in terms of the quality of product and the services that we can offer,” said Green Point UK and Bitzer UK’s md Kevin Glass.
Employing engineers trained at Bitzer’s master Green Point facility and under the guidance of new Green Point UK general manager Will Pribyl, the process will include the replacement of the existing motor with a brand new one as well as completely new valve plates, bearings, piston rings, bearings and pressure relief valves. The Green Point Quality kit contains all the critical safety, wear and tear parts.
Each compressor that arrives will be documented and analysed to determine the possible root cause of failure. It is then repaired and the replacement of parts is carried out only after careful evaluation and not randomly. Components still in good condition are checked, cleaned and repositioned whilst lubricant, washers and gaskets are always replaced to help ensure safe and reliable operation. They are fully tested before despatch and Green Point UK is equipped with a dedicated bench test facility to check the operational efficiency of the repaired compressor against those of an original new compressor.
According to Kevin Glass, Bitzer’s own tests have shown that poorly remanufactured compressors can be at least 10% less efficient – often due to the use of a rewound compressor. Bitzer insists that it will only use new motors and new valve plates in all its remanufactured units.
In addition, only Bitzer parts will be used. In the case of other manufacturers’ compressors original parts will be used where available or alternatively quality approved pattern parts that meet oem tolerances and specifications.
A lift and shift service will also be offered.
Green Point UK’s website www.greenpointuk.co.uk will provide customers with comprehensive real time information on remanufactured stock availability as well as comprehensive details of the services on offer.