The flagship for advanced climate control
1st June 2014Raising Henry Vlll’s warship the Mary Rose in 1982 demanded care and precision. The closely-controlled conditions now being demanded for its preservation are equally uncompromising.
It was the pride of the English fleet when it sank in 1545. Raised again in 1982, the remains of Henry Vlll’s warship the Mary Rose has since been undergoing the most advanced and expensive preservation techniques to prevent the recovered 20m x 13m section crumbling to dust.
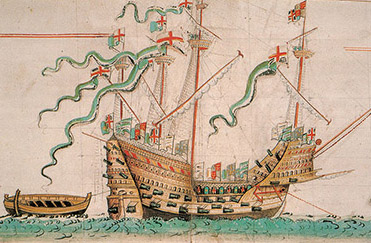
Now encased in its own purpose-built museum (the museum was actually built around it) in Portsmouth’s historic dockyard, the Mary Rose is relying on the latest in climate control technology to help preserve the legendary vessel for future generations.
Initially sprayed with chilled water to stabilise the timber, for the past 10 years the ship’s timbers have been treated by spraying with polyethylene glycol. The ship has now entered its final phase of conservation to allow the timbers to dry which will take a further four to five years.
Three Airedale air-cooled packaged chillers, three Eaton Williams air handling units using Fanwall technology and three Vapac humidifiers are being used to provide the right conditions for the preservation and drying out process.
During this time almost 100 tonnes of water will be extracted from the timbers, while the hull is contained in what the conservationists have dubbed the ‘hot box’ – in reality a closely-controlled environmental chamber. The conditions being maintained within the hot box are 19C (+/-0.75C) and 54%RH (+/-4%).
Windows have been installed in the hot box with viewing galleries running the length of the ship.
Once the drying process is completed the hull will contain approximately 12% of moisture. The glass will be removed and visitors will enjoy open views of the hull.
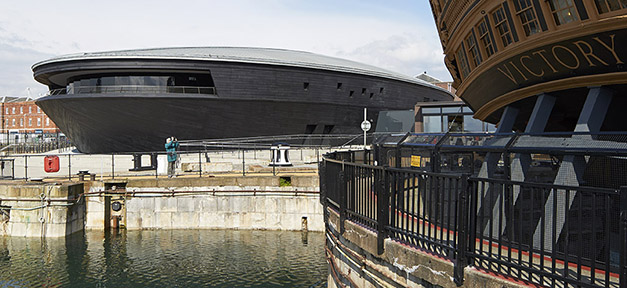
Specifying an effective air handling and humidifier solution was not without its difficulties. Space constraints dictated that any solution would need to be situated in the west dock plant room of the museum with the bulk of equipment in the dry dock, where access was limited.
The critical nature of the museum required 24/7 operation, built in redundancy, low noise levels and crucially a small footprint and modular construction.
The Trust looked at several options including an N+2 solution, but this proved costly and unworkable because of the location and restricted space.
“Access, limited space, size constraints and 24/7 reliability were key considerations,” commented professor Mark Jones, head of collections at The Mary Rose Trust. “The museum cannot be disrupted. We required a robust solution that could offer N+1 redundancy, facilitated ease of maintenance as well as Part L compliance.”
“Any plant failure would be detrimental and put undue stress on the timbers. We adopted a ‘what-if’ approach with Eaton-Williams,” explains professor Jones. “It was essential that any solution could not be compromised.”
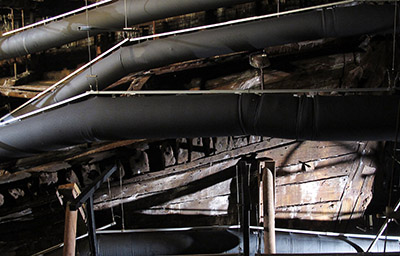
Fanwall’s technology, using small diameter fans in an array (six in each unit) instead of a single fan used by traditional air handlers, ensures that when a fan fails the others will compensate and if any of the other AHUs fail the remaining systems can operate at a greater capacity to ensure that the preservation process continues uninterrupted.
The units were constructed at Eaton-Williams plant in Stoke-on-Trent and rigorously tested for air leakages and volume testing. The systems were then dismantled and delivered to the site where they were constructed in the dry dock.
The Eaton-Williams Fanwall systems used to facilitate the drying process will provide an initial drying duty of 8.33 m3/s with a final duty 7.5 m3/s and a standby duty of 12.5 m3/s. There are heating and cooling coils in three sections and even at peak duty only two out of three coils are required to meet the load
Four LKP air handlers will provide the galleries with comfort cooling at 18-24°C with ambient RH, with duties ranging from 1.92 m3/s in the east gallery, to 2.16 m3/s in the west gallery.
To ensure even distribution of air during the drying period, the Mary Rose Trust has employed fabric ducting from KE Fibertec.
Vaisala humidity sensors are employed to ensure constant conditions are met and all systems are controlled by a sophisticated demand-led building management system.
“Temperature and humidity will be very carefully controlled using Fanwall and Vapac humidifiers, even when The Mary Rose is fully dried out, to ensure that all the artefacts are preserved in perpetuity,” said professor Jones.