Success is in the pipeline
11th September 2015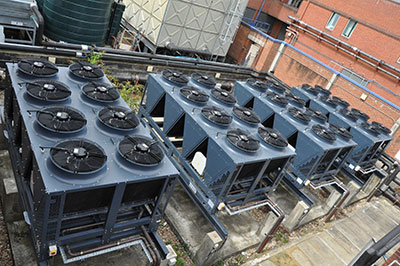
UK: An unusually long underground run of refrigerant pipework has been employed in a major R22 chiller replacement project at Salisbury Hospital.
Four new R134a Turbomiser chillers, with a combined cooling capacity of around 1.4MW, are connected to air-cooled condensers by DX pipework up to 75m in length. The large-gauge copper tube (up to 3⅝ on the discharge and 2⅝ on liquid lines) runs beneath a road in a concrete-lined culvert.
The installation, which took nine weeks to complete, required refrigerant pipe to be mounted on custom-fabricated brackets every 1.5m along the length of the underground structure. Each chiller and condenser is on an independent circuit.
The Turbomiser chillers replace four 20-year-old R22-based Hitachi chillers with dual screw compressors. Although they were installed on the existing mounting points, they occupy two-thirds the space.
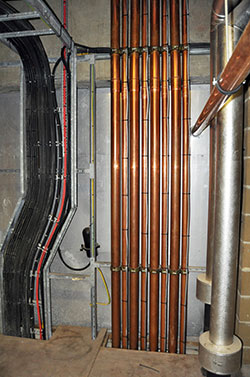
The Turbomisers, fitted with an Economiser based on a high efficiency brazed-plate heat exchanger, provide cooling for the hospital’s air handling units, serving wards, administration areas and waiting rooms. They are linked to a hospital-wide BMS, with control based on return-water temperature. The BMS controls chiller sequencing and run-time to even-out operational hours and prolong working life.
Cool-Therm provided a complete turnkey installation, including design, supply, installation and commissioning. The company has also secured a five year service and maintenance contract for the chillers.
In a previous project at the site, Cool-Therm supplied a packaged air-cooled Turbomiser chiller, complete with integral condenser, enabling it to be located in a restricted space in an enclosed area of the hospital.
Rob Young, Cool-Therm project director, said: “Due to the need to maintain continuity of cooling throughout, it required a carefully managed staged approach. Because of the time of year, we were able to remove three of the four original chillers and leave one operational, after ensuring it was capable of meeting all anticipated demand.
“When two of the three new systems were operational, the fourth original unit was decommissioned and removed, and the final chiller and associated condenser installed.”
He added: “The need to route pipe work under a road and a delivery area obviously added an extra dimension, and one that we had not encountered before. However, the custom-designed mounting system we developed proved very effective.”
The Cool-Therm installation team was led by Simon Umlandt, assisted by Steve Baker and Andy Comerford.
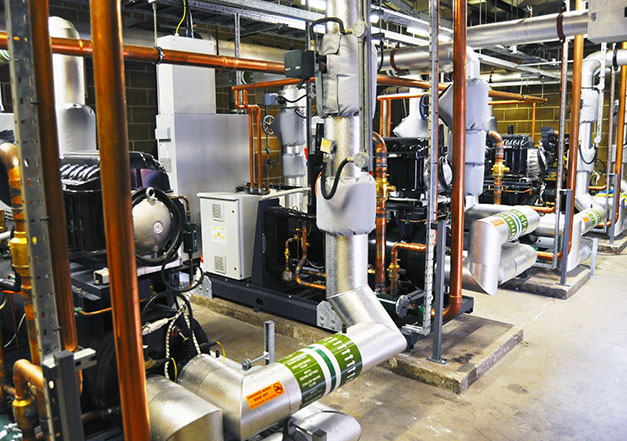